A little time was spent in the shop before preparing for church (yes, we attend 2 services per week - with my mum & mum-in-law on Saturday for either the Hokkien or Mandarin Service and on Sunday for our English Service).
I finished the arbor with a thread hole to mount the partially completed 1/2 centre and fastened the threaded end of the 1/2 centre in it. This is what I have:
It wobble like no tomorrow. I therefore declared this to be good for the scrap bin.
I do not have another piece of silver steel in my stash bin and thought of using the piece of silver steel meant for the 2 adjustment screws that came with the kit. The 5/8" diameter silver steel rod supplied is slightly longer than 5". Each adjustment screws is only slightly longer than 1". Then it struck me that the extra length is meant to be use to make the arbor... Argghhh... I'll cut a short section of 1.5" to make the 1/2 centre.
 |
The much trusted 3 jaw chuck is now in use. |
 |
Facing the end square to prepare to turn slightly under 1.5" length to 0.5" diameter. |
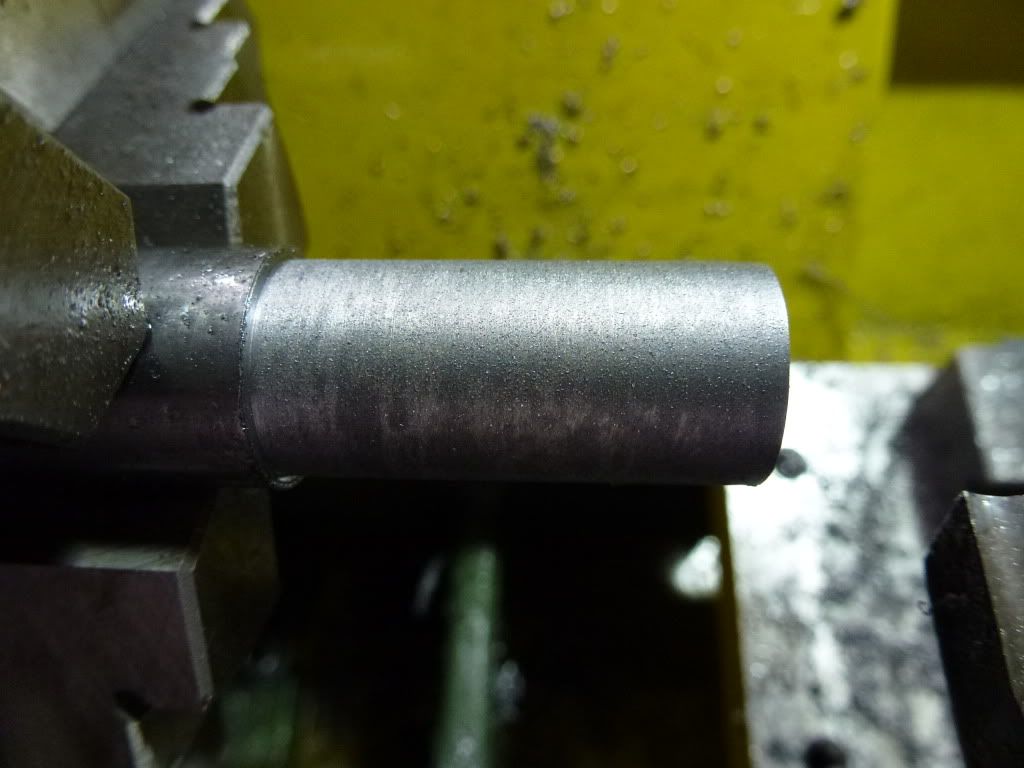 |
The finishes came as a surprise. It was so rough and looks the textual on a diamond file... |
I stop work right away, not wanting to carry on till I figure this out. The silver steel was turned with the HSS tool from Proxxon. I tried turning with and without oil, spindle speed of 330 rpm and 660 rpm, advancing the tool 0.1mm to 0.4mm radius, feed slow, fast, and with autofeed. The rough surface remains...
Anyone can provide me with a solution to this and the reason why this occur? Appreciate any help.
- Posted using BlogPress from my iPhone